Running a warehouse is an expensive, time-consuming and complex activity. This is why, often, businesses outsource their logistics, relying on 3PL companies to take care of warehousing operations and customer orders. These companies ensure that all operations are efficient, from picking and packing to delivery and returns, and that storage space is organised properly. How do they do so? 3PL providers equip businesses with the tools and technology necessary for optimising operations to their fullest potential. A partner like eLogy, for example, does so by providing physical means (warehouses and transport fleet) empowered by advanced technology. This is a key benefit for ecommerce businesses, as it offers significant cost reductions, faster operations and accelerates growth. Utilising a 3PL means having a solid ecosystem to manage all operations seamlessly, adapting quickly to market fluctuations, enhancing competitiveness, and efficiently meeting consumer demands. In this context, we have all heard about an indispensable component called a Warehouse Management System (WMS). But who really knows how it works? Let’s discover how a WMS works and all processes it manages.
WMS meaning: what is a Warehouse Management System?
A WMS is a tool that gives warehouse teams full visibility into inventory and operations, while automatically managing warehouse processes from receiving and distribution to data collection. A WMS software simplifies the management of warehouse operations, enhancing efficiency by providing real-time inventory level data, as well as order status. Let’s take a look at WMS functions more in depth:
- Reception and inventory storage: A WMS simplifies the receiving and storage process by categorising and recording incoming stock.
- Inventory tracking: a WMS keeps track of inventory levels, preventing errors that could lead to significant sales losses or fulfillment delays.
- Order preparation and packaging: A WMS automates the creation of picking lists and shipping labels, allowing teams to fulfill orders accurately and deliver to customers more quickly.
- Shipment tracking: A WMS allows both businesses and customers to track orders in real-time, offering a more transparent and reliable service.
- WMS analytics: An advanced WMS generates reports and analytics on warehouse and order performance, allowing businesses to plan and refine warehouse processes thanks to actionable insights. Check out the most important warehouse & fulfillment KPIs to track the performance of your warehouse processes and plan strategies accordingly.
WMS benefits in numbers
50% less travel time for forklifts, thanks to system-directed pick and pack strategies
27% less inventory costs in automated warehouse environment
35% less operating expenses
Here’s a step-by-step overview of how a WMS typically works:
- Once inventory arrives at the warehouse, the WMS automatically records items in the system through barcode scanning or RFID tags on the SKUs. In this way, operators are always able to track the exact quantity and location of each item, ensuring inventory is always updated in real-time and manual errors are minimised.
- The WMS automatically assigns a storage location for each SKU by analysing the size, weight and selling frequency of each item. Typically, fast-moving items will be located near shipping areas for maximum efficiency.
- The WMS records the exact location of each item and tracks every movement, allowing operators to see when its place is changed, it is sold or shipped, and updates all information in real-time.
- Once a customer orders a product or multiple products online, the WMS generates a picking list to fulfill the order. Also, it automatically generates shipping labels, so that carriers have the most accurate information. This is one of the most expensive stages of warehouse operations, accounting for at least 55% of total operating costs. So, optimisation at this stage can lead to significant cost savings.
- The WMS collects data to generate reports and analytics that provide insights into all warehouse operations, like order fulfillment accuracy, inventory levels, warehouse expenses, and demand forecasting. This allows businesses to identify areas for improvement, thanks to data-driven insights. furthermore, they save money by eliminating disruptions and preventing overstocking and understocking situations.
What features does the perfect WMS have?
Cloud based WMS
A cloud-based WMS is cheaper and ensures more operational continuity, since it is web-based. This means it does not require server hardware or synchronisation with server hardware and networks. It is therefore more simple to use and is more flexible in case a business needs to scale its operations. Storing and inventory data on a cloud-based Warehouse Management System (WMS) offers an extra level of security, because it separates warehouse information from actual production information. Teams can easily access the information from anywhere and, in case of disruptions, a cloud-based WMS ensures that all critical data, including order details and tracking information, is securely backed up.
Order tracking
Order tracking is a necessary feature for every ecommerce! Customers and brands expect an extra level of visibility, being able to track the progress of their orders at every stage of the fulfillment process. Every ecommerce brand must let buyers know when to expect their packages.
Moreover, a WMS gives real-time inventory updates, so that customers are always informed and owners aren’t surprised by sudden stock run-outs.
Editing orders
Another WMS benefit is that it allows warehouse staff and customers to easily make changes to orders, offering a more flexible shipping process. For example, if a carrier rate changes, a WMS can automatically select the carrier with a more competitive tariff.
Returns management
Returns can easily disrupt a warehouse, especially if there is no real-time visibility across all processes and if many operations are carried out manually.
A WMS enhances transparency by automatically informing customers on the progress of their returns and refunds. Furthermore, once returns are processed, a WMS updates inventory levels in real-time, eliminating so called “ghost inventory” — items that are not physically present in the warehouse but shown “in stock” or available – a situation which leads to missed sales and dissatisfied customers.
Analytics, demand forecasting and reporting
One of the most important features of a WMS is its ability to keep track of data, generate real-time analytics, create accurate reports, and provide demand forecasting insights. This is a precious tool for businesses, as it allows them to plan strategies based on real, precise data to direct their marketing efforts more accurately, improve low-performing areas, and plan stock levels adequately to meet customer demand.
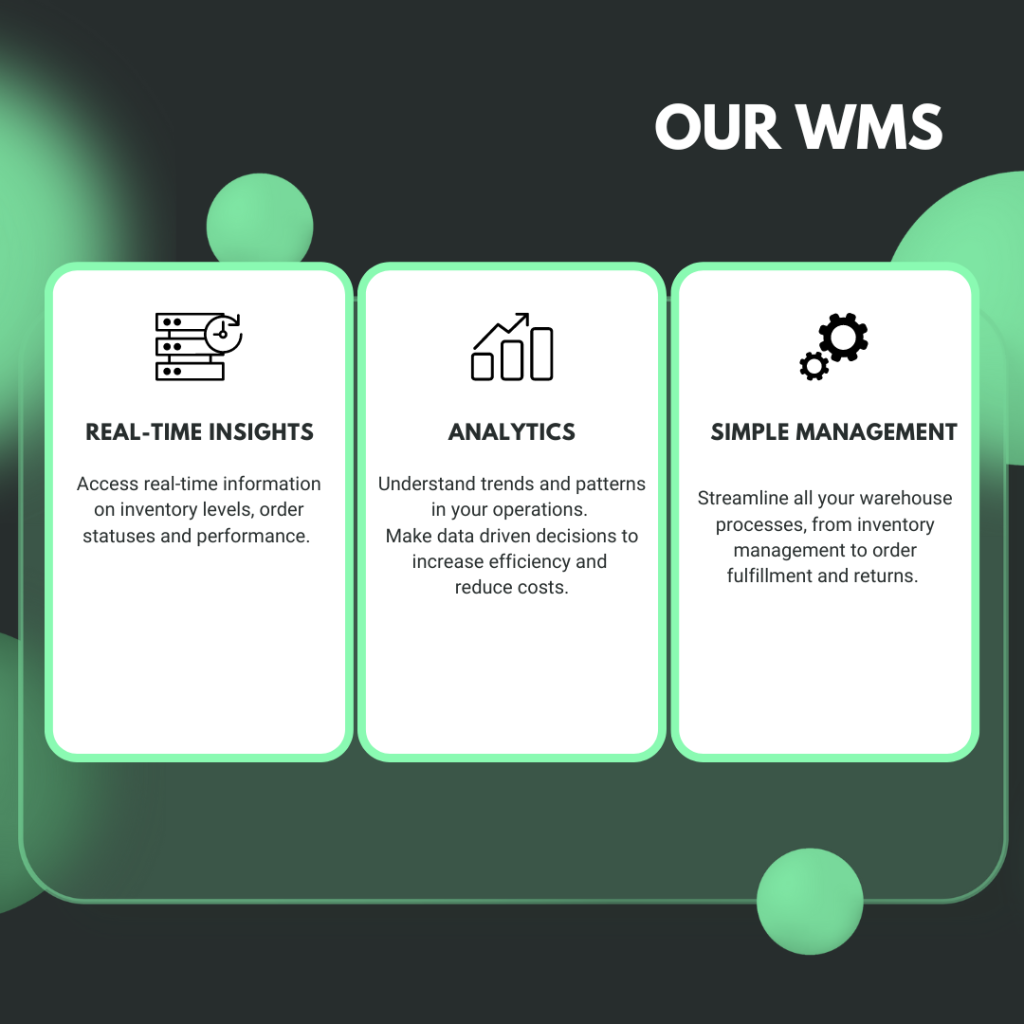