Inventory Accuracy is a Key Performance Indicator (KPI) essential among logistics data and measures the degree to which the inventory recorded in the system aligns with the actual stock present in a warehouse. This inventory management KPI helps businesses improve the efficiency of their supply chain, directly impacting customer satisfaction. Let’s discover how to achieve high levels of Inventory Accuracy to prevent stock shortages and reduce excess inventory.
The importance of maintaining optimal Inventory accuracy
When the recorded inventory data does not align with the actual physical stock present in the warehouse, it can lead to a series of negative situations, like backorders and delays. This will have serious repercussions on your brand reputation and impact the reliability of your business. In fact, if customers order on your website, thinking they will receive a desired product soon, and shortly after they discover that the item is out of stock, they will not come back to shop from you again. This will lead to lost sales and bad word of mouth.
Let’s consider an example of a fashion boutique that begins the month with an inventory of 100 handmade hats. If it sells 20 hats, inventory should show 80 remaining hats. However, let’s suppose a manual conducted count only shows 75 hats in stock. This discrepancy reflects a series of issues that have to be addressed immediately. Discrepancies in Inventory Accuracy can result in stock shortages, delays in order fulfillment, and errors in shipments, leading to customer dissatisfaction and eroding their trust in a company.
Enhancing Inventory Accuracy goes beyond mere numbers; it’s about meeting customer expectations, reducing expenses, and optimising operations. Closely monitoring Inventory Accuracy empowers businesses to make well-informed decisions about stock procurement and distribution of products.
How do you calculate Inventory Accuracy?
You can calculate Inventory Accuracy using the following formula:
Inventory Accuracy (%) = (Actual Inventory / Recorded Inventory) x 100
What is a good Inventory Accuracy rate?
Realistically speaking, achieving a perfect inventory accuracy rate of 100% is almost impossible. It is normal that sometimes recorded inventory doesn’t match what is in the warehouse. However, ideally, businesses should maintain the ratio over 92% as much as possible.
Overstocking and understocking
When inventory counts are not accurate, businesses either accumulate excess stock or experience a shortage of products. Both are situations to avoid, because having too much stock consumes money and space resources, while not having enough stock leads to lost sales and dissatisfied customers.
Customer loyalty
For an ecommerce business, customer loyalty is one of the most important aspects to invest in. In fact, it helps to boost profit margins by focusing on increasing the value of existing customers, rather than spending resources on the ceaseless pursuit of new clientele, only to be trapped in a repetitive cycle of gaining and then quickly losing customers.
Discrepancies in inventory counts disrupt order fulfillment processes, causing delays in delivery, incorrect items being sent, or even order cancellations, consequently frustrating customers and diminishing their trust in a brand. On the contrary, maintaining high Inventory Accuracy levels is essential to ensure precise and accurate order fulfillment, contributing to a high quality customer experience, encouraging customer loyalty, and promoting repeat business.
Leveraging technology can dramatically improve a brand’s ability to maintain optimal Inventory Accuracy levels and enhance efficiency across all warehouse operations. Key technologies include warehouse management systems, real-time tracking solutions, and automation tools.
Enhancing Inventory Accuracy with Warehouse Management Systems
Inventory Accuracy is a complex challenge for ecommerce businesses, especially when they opt for self-storing solutions and fulfill orders directly from their premises. Complications often arise when storage is not handled within a dedicated warehouse environment.
In fact, as order volume grows and as businesses diversify their product offerings, the complexity of managing inventory rises if they don’t have adequate tools, premises, and an expert team in place.
Also, ecommerce businesses often rely on manual inventory record-keeping, or lack tracking systems.
Adopting advanced WMS technology is crucial for a successful business. Warehouse Management Systems (WMS) offer a robust, reliable solution for managing and keeping record of every inventory movement by automatically tracking and reporting variations. These systems eliminate manual errors, automate the collection of data, offer full visibility of operations within the warehouse, and allow for real-time updates to inventory levels on all sales channels. Adopting a WMS not only increases levels of Inventory Accuracy but also enhances supply chain performance. In fact, the likelihood of human errors is reduced to bare minimum and thanks to automatic order processing, stock replenishment, and data collection overall warehouse operational efficiency is improved.
How eLogy can help
eLogy helps brands achieve and maintain high Inventory Accuracy levels thanks to its warehousing and fulfillment network, powered by cutting-edge technology.
eLogy’s fulfillment platform easily connects with your ecommerce marketplaces or website, offering a complete overview of stock and every movement of products entering and exiting your warehouse. Brands can track their inventory in real-time, receive alerts for low stock levels, and gain insights to forecast future inventory demand.
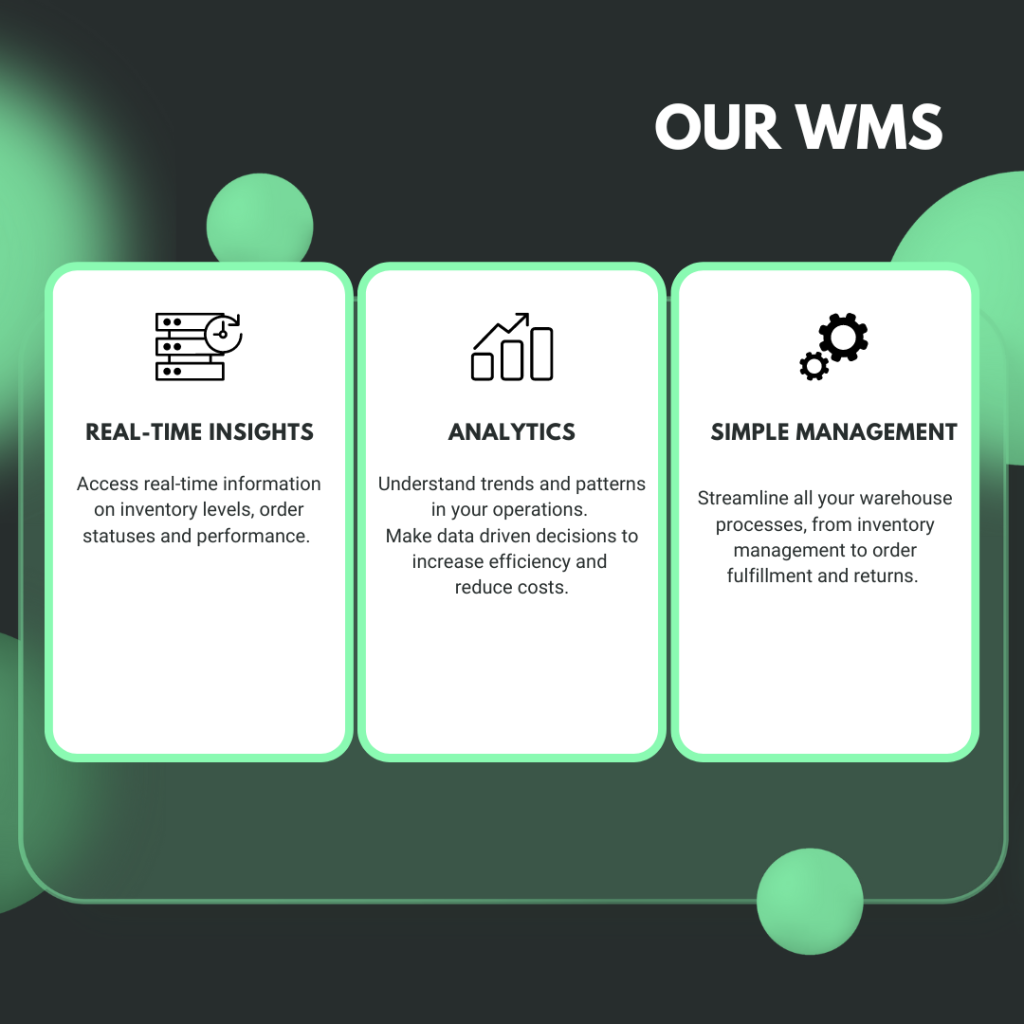